This article will be talking about general information about the filling level measurement with an overview of five different measurement methods that Burkert has to offer.
Definition
Filling level measurement involves determining the filling level of media in industrial containers, such as process and storage tanks, silos or open channels. This is achieved by converting measured values into electronic signals. The signal issued is integrated into the control circuit of the relevant process control system. In this context, a distinction is made between continuous measuring methods and limit value sensors. The following section sets out to explain the various types in greater detail and to highlight the advantages of the principles.
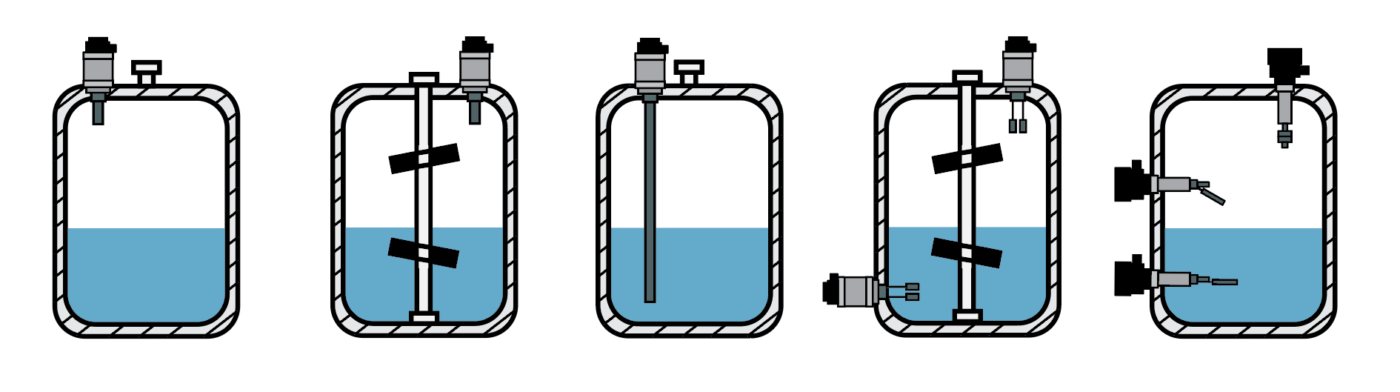
Types of Filling Level Measurement
Continuous Measuring Methods:
Ultrasonic Level Measurement
The transmitter emits an ultrasonic wave at a surface, which then reflects the signal. By using the signal delay time, the device can calculate the distance from the sensor lower edge to the surface. The influence of the speed of sound, which itself is dependent on the surrounding atmosphere, is automatically compensated for by the transmitter based on the input of specific values and measurement of the ambient temperature.
If the distance between the sensor lower edge and the bottom of a container is known, the device can display the fill level. If the container geometry is known, then the volume can also be determined. With the help of various disturbance echo filters, the system can also be used inside containers – even if built-in fixtures generate disturbing echoes. Since there is no direct contact with the medium, the sensor enables applications with strict hygiene requirements. They are usually used in open basins, wastewater applications, and silo or tanks of chemical and dairy plants.
Take measurements in:
- Liquids
- Paste-like media
- Powders
- Bulk materials
Advantages:
- Measurement is performed independently of media properties
- Suitable for abrasive and aggressive media thanks to non-contact measurement
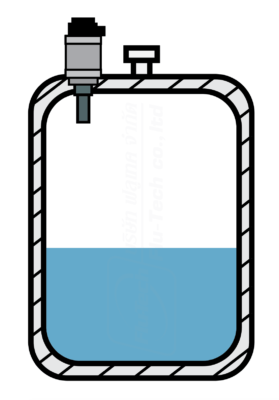
Radar Level Measurement
The radar measuring device consists of a housing containing the electronics, a process connection with an antenna and a sensor. The radar sensor transmits brief radar pulses with a duration of approximately 1 ns from the antenna. These pulses are reflected by the filling material and received by the antenna as echoes. Radar waves are propagated at the speed of light.
The delay time of the radar pulses from transmission to reception is proportional to the distance and therefore to the filling level. The filling level determined in this way is converted into a corresponding output signal and issued as a measured value.
The filling level sensors are frequently used for aggressive media as well as dynamic process conditions, such as high temperatures or pressure fluctuations. As with the ultrasonic measurement, the measurements in this case are performed without contact. Since no direct contact with the medium is required, the measuring principle is ideal for hygienic applications.
Production processes for yoghurt products run in a controlled manner in highly sterile environments. This places particular demands on the cleanability of all parts coming into contact with the medium. Consequently, the cleaning processes used are extreme because any contamination by external bacteria results in the loss of the entire batch. The non-contact radar principle is impervious to the changing density of the yoghurt and remains unaffected by abrasion due to the fruit. The radar measuring device detects the current filling level and forwards this to the control system. Even the circulating agitators and prevailing vapor atmosphere do not interfere with the measurement.
Take measurements in:
- Liquids
- Paste-like media
- Powders
- Bulk materials
Advantages:
- Highly accurate measured values
- Ideal for dynamic process conditions
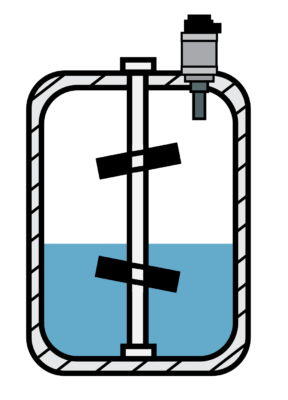
Guided Radar Level Measurement
High-frequency radar signals are guided along a bar or a steel cable. As soon as the media surface is reached, these waves are reflected and received by the sensor. Based on the delay time of the waves, the filling level is determined and issued as a measured value.
Advantages:
- Precise level measurement up to 75 meters
- Fast commissions due to pre-configured probe lengths
- Liquid interface measurement possible even with density flunctutations
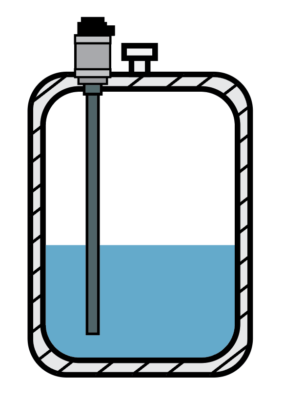
Limit Level Detection:
Float Switch
A floater is a type of sensor whose low density allows it to float on the surface of the liquid. Inside the floater, there is a magnet as well as one or more reed contacts. When the defined filling level is reached, the buoyancy causes the magnet to activate the reed contacts. In the process, measurement is carried out independent of influences such as pressure, temperature, conductivity and bubble formation in the media. As a result, the principle can be used for various applications such as in foaming media or dynamic surfaces as well as across wide temperature ranges.
Take measurements in:
- Liquids
Advantages:
- Various mounting positions possible
- Tolerant against dirt particles within the medium
- Wide range of applications, such as with aggressive liquids
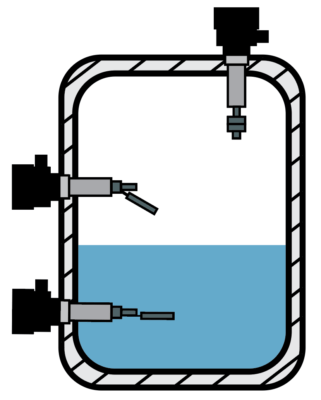
Tuning Fork
A tuning fork is installed in the tank. This tuning fork is s energized piezo-electrically and oscillates at its mechanical resonance frequency of approximately 1,200 Hz. The oscillation frequency changes in contact with media. The frequency change is detected by the integrated oscillator and converted into a switching command.
Advantages:
- Fast commissioning
- Ideal for liquid level measurement
- Suitable for the most difficult measuring conditions
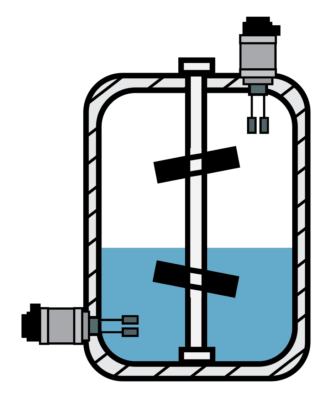
Related Products
Reference: Burkert
For more information:
Tel.: 02-384-6060 | Line: @flutech.co.th | Email: [email protected] | Facebook: @flutech.co.th | Website: https://flutech.co.th