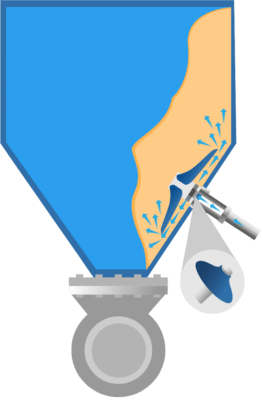
Fluidizers have less power, smaller activation area, need more accessories, and consume more energy.
Is it really the “cheaper” flow aid?
Fluidizers are a pneumatic flow aid that use a combination of aeration and gentle vibration to promote material flow. The discs force air to move along the vessel wall, which loosens the material and prevents it from plugging or becoming compact.
Fluidizers are often used in storage silos, hoppers, and dust control systems. They can be installed outside or inside the vessel, and are usually made of silicone or EPDM rubber.
FLUIDIZERS: USES AND APPLICATIONS
Fluidizers work best with dry bulk materials that respond to gentle aeration, or have a moisture content that is less than 12 to 15 percent. There are models designed for either low-pressure/high-volume and high-pressure/low-volume air, but they generally have less power and a smaller activation radius than other flow aids.
Fluidizers are used to prevent ratholing and bridging in silos and other storage containers, or to promote discharge from transportation like dry bulk trailers.
FLUIDIZERS: PROS AND CONS
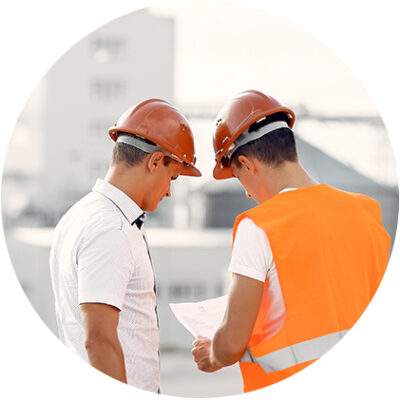
Fluidizers are inexpensive and easy to install, since they only require a small hole for the discs. Some vessels already come with pre-fitted fluidizing systems.
But while the initial costs are low, fluidizers may not be as cost-effective as they seem.

Limited activation radius. You may need more units to achieve the desired results.

Frequent replacement. They degrade quickly. Even slightly uneven edges can lead to inconsistent airflow or affect its ability to seal tightly against the vessel walls. In these cases, the fluidizers must be replaced.

Frequent visual inspections and cleaning. Material can cake or harden underneath the discs.

Ineffective for some materials. Fluidizers can only activate dry powders or light solids. They can’t be used for large particles like gravel, interlocking particles like wood shavings or fiberglass, or moist or dense material like whey.
Reference: AirSweep®